The Main Earthing Terminal (MET) is a crucial component in an electrical installation that serves as a central connection point for all earthing conductors within a system. It ensures that all parts of the installation have a common ground reference, which is essential for safety, equipment protection, and compliance with electrical standards.
Functions of the MET:
-
Electrical Safety:
- It provides a pathway for fault currents to flow safely to the ground, reducing the risk of electric shocks or fire.
-
Common Connection:
- It interconnects all earthing systems, such as the protective earthing (PE), equipotential bonding, and functional earthing, into one unified system.
-
Fault Management:
- It facilitates the safe disconnection of protective devices (like circuit breakers or fuses) by providing a low-impedance path to the ground during faults.
-
Compliance:
- It ensures the electrical installation complies with relevant safety standards, such as IEC, NEC, or BS standards.
Components Typically Connected to the MET:
- Protective Earthing (PE) Conductors: Connects metal parts of equipment to the MET.
- Equipotential Bonding Conductors: Links different metallic systems (e.g., water pipes, gas pipes) to prevent potential differences.
- Main Earth Electrode Conductor: Connects the MET to the physical earth (via earth rods, plates, or other electrodes).
- Lightning Protection System: Ensures safe dissipation of lightning strikes.
- Functional Earthing Conductors (if required): For grounding certain electronic components or systems.
Location of the MET:
The MET is usually located near the main distribution board, where the incoming supply enters the building. In larger installations, it may be part of the Main Earthing Bar (MEB) or Earth Bar, which serves a similar function on a larger scale.
Standards and Best Practices:
- The MET must be robust, corrosion-resistant, and capable of handling high fault currents.
- It should be easily accessible for maintenance and testing.
- Clear labeling and proper segregation of conductors are required to avoid confusion during inspection or troubleshooting.
The MET is a foundational element in ensuring the electrical safety and reliability of any installation.
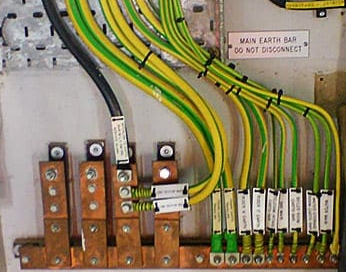
0 Comments